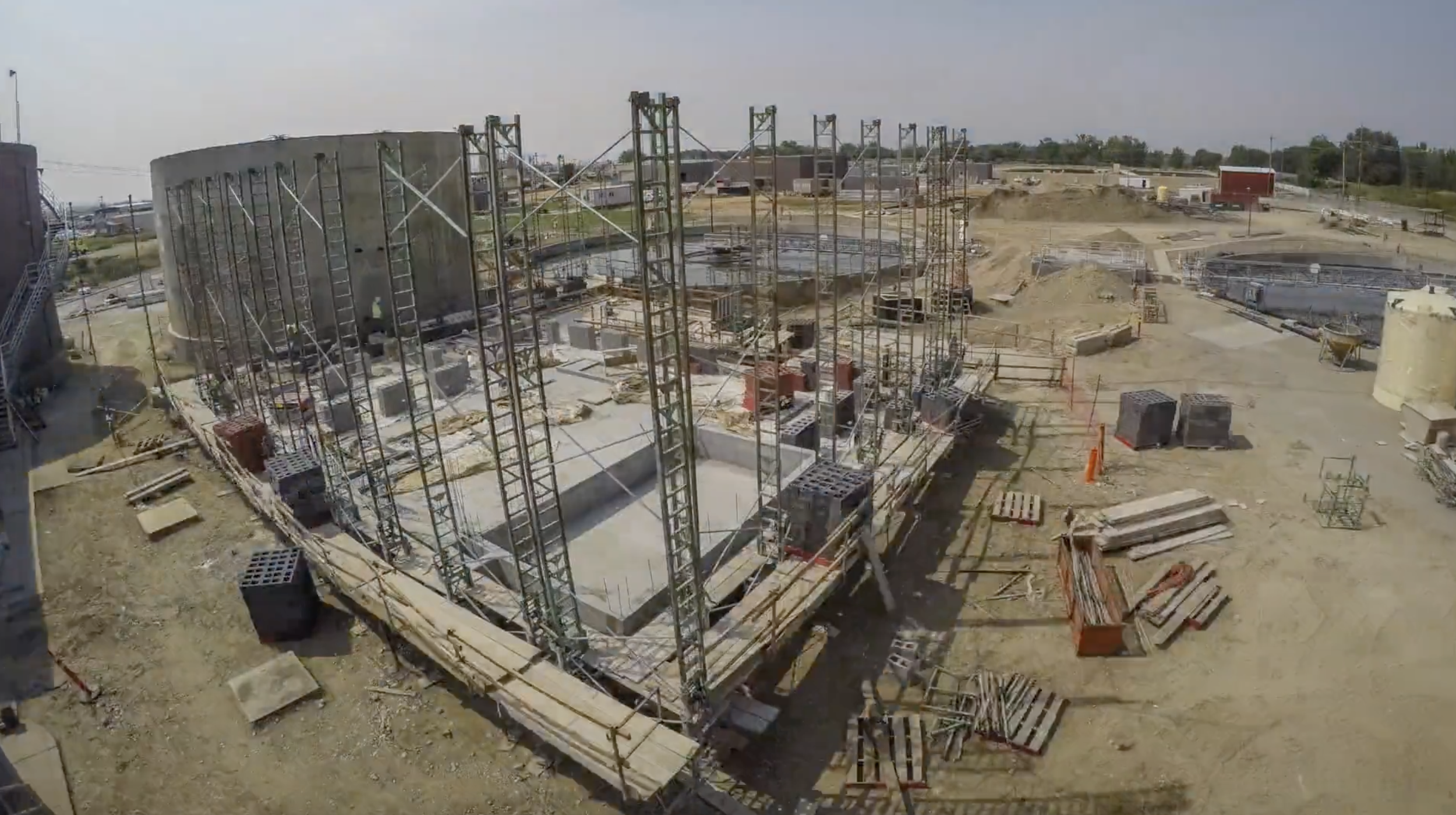
CALDWELL DIGESTER
DEMOLITION , process piping and equipment, STRUCTURAL SOLUTIONS
THE CALDWELL DIGESTER was very technical as it required to maintain the plant fully operational during all the construction phases.
Caldwell Digester project was safely and successfully completed mid-2018. This project was an upgrade to the existing Caldwell WWTP by demolishing the existing two digesters and old control building. We replaced them with a new Digester and new control building. This project was very technical as it required to maintain the plant fully operational during all the construction phases. This project was very technical in the replacing of the outdated Control Building with a new Control Building. Most of the power and control for the entire plant came through the old Control Building. JCC’s strengths were at center stage to enable the Control Building demolition. Beginning several weeks before bid day, many months of pre-planning, flow charting and selective demolition were required in the successful removal and bypassing of critical plant control systems housed in or passing through the old Control Building. Also complicating the demolition was the Sludge Pump Room, which needed to stay in service until the new long lead time sludge pumps arrived and could be installed. Further still, the old Sludge Pump room was in the basement footprint of the new Control Building.
With bypassing mostly complete, JCC demolished most of the Control Building and two existing and outdated Digesters. The new site piping and the new Digester excavation got underway. The existing Sludge Pump room remained, old pumps were made temporary, and a permanent basement retaining wall was constructed to allow the new Control Building to get underway. Now seven months into the project, JCC got the 24” thick heavily reinforced base slab under way for the Digester. 24” thick walls began to rise in two lifts, first to 7’ high, then another 28’ high. Finally, JCC shored and placed the heavily reinforced concrete deck at 35’ above the base slab. Parapet walls followed while an interior protective lining went in. A CMU veneer was installed, and last, a JCC fabricated aluminum radial stair case went to the top.
Soon after the Digester base slab placement, the extensive under slab Control Building piping got underway and the building basement footings were placed. Predictably, the new Control Building housed much equipment, including a basement Sludge Pump Room of its own. Also included were a boiler, two heat exchangers, more pumps, many plant systems, a central MCC and control. Upon completion, the new Control Building was packed full of process equipment and process piping, hydronic piping and gas piping, all appearing as a well-coordinated work of art.
Our strengths were really shown during the technical pre-planning and execution of plant integration.
-
JC Constructors has completed demolition of environmentally sensative materials such as concrete, asebestos, and lead paint around clear waters, habitats for threatened and endangered species, and other environmentally sensitive areas.
-
Process piping and equipment are a significant portion of most contracts JCC pursues. They nearly constantly have work progressing, both on mechanical piping and equipment procurement and installation. JCC’s process work has included treatment from potable water to municipal wastewater, sludge handling and industrial pre-treatment.
-
JCC employs an extremely skilled team of men producing very complicated, often corrosion resistant metal fabrications. From pressure piping manifolds to ascending radial stairs to large fabricated lids, the JCC fabrication team has been able to support almost any fabricated project requirement.
-
JCC has constructed structural concrete for transportion structures, water treatment, and wastewater treatment.
WHERE OUR EXPERTISE CAME IN
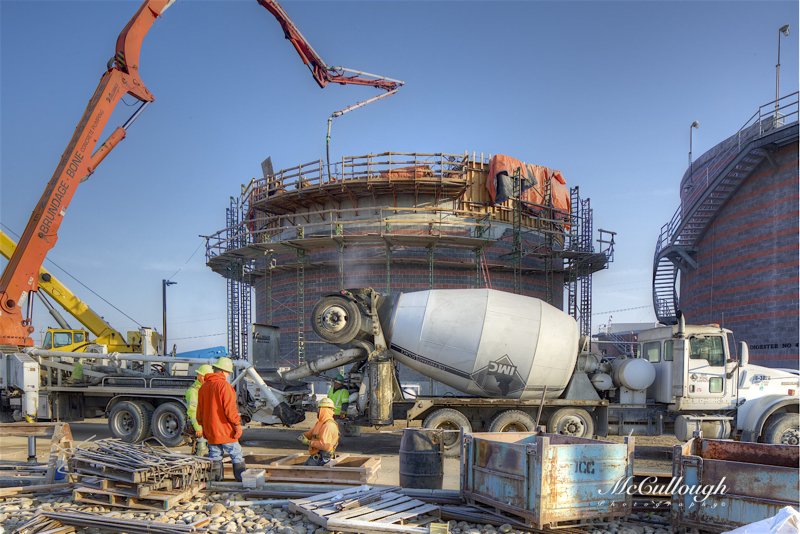
